焊接機(jī)器人對(duì)零部件的定位精度要求較高
來(lái)源:http://meangen.com/ 發(fā)布時(shí)間:2021-08-16 瀏覽次數(shù):0
焊接機(jī)器人是集機(jī)械、計(jì)算機(jī)、電子、傳感器、人工智能等多個(gè)方面知識(shí)于一體的自動(dòng)化裝備。焊接機(jī)器人主要由機(jī)器人本體和自動(dòng)化焊接設(shè)備兩大部分構(gòu)成。
Welding robot is an automatic equipment integrating machinery, computer, electronics, sensors, artificial intelligence and other knowledge. Welding robot is mainly composed of robot body and automatic welding equipment.
1、焊接機(jī)器人的主要優(yōu)點(diǎn)體現(xiàn)在:
1. The main advantages of welding robot are as follows:
①穩(wěn)定和提高焊接質(zhì)量,保證其均一性;
① Stabilize and improve welding quality and ensure its uniformity;
②提高生產(chǎn)率,機(jī)器人可做到24小時(shí)焊接;
② Improve productivity, and the robot can weld for 24 hours;
③改善勞動(dòng)條件,可在有害環(huán)境下持續(xù)工作;
③ Improve working conditions and be able to work continuously in harmful environment;
④可實(shí)現(xiàn)中、小批量的焊接自動(dòng)化。
④ It can realize medium and small batch welding automation.
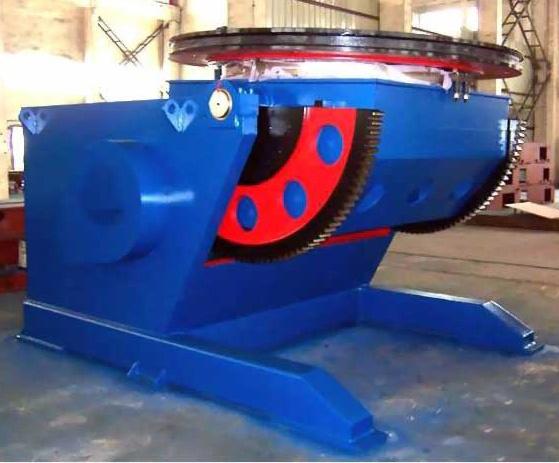
基于上述優(yōu)點(diǎn),焊接機(jī)器人在汽車制造及零部件領(lǐng)域得到了日益廣泛的應(yīng)用。目前廣泛使用的焊接機(jī)器人都屬于一代工業(yè)機(jī)器人,它的基本工作原理是示教再現(xiàn)。示教也稱導(dǎo)引,既有用戶導(dǎo)引機(jī)器人,一步步按實(shí)際任務(wù)操作一遍,機(jī)器人在導(dǎo)引過(guò)程中自動(dòng)記憶示教的每個(gè)動(dòng)作的位置、姿態(tài)、運(yùn)動(dòng)參數(shù)、工藝參數(shù)等,并自動(dòng)生成一個(gè)連續(xù)執(zhí)行全部操作的程序。完成示教后,只需給機(jī)器人一個(gè)啟動(dòng)命令,機(jī)器人將準(zhǔn)確地按示教動(dòng)作,一步步完成操作。
Based on the above advantages, welding robot has been widely used in the field of automobile manufacturing and parts. At present, the widely used welding robots belong to a generation of industrial robots, and its basic working principle is teaching and reproduction. Teaching is also called guidance. The user guides the robot and operates it step by step according to the actual task. During the guidance process, the robot automatically remembers the position, attitude, motion parameters and process parameters of each action taught, and automatically generates a program that continuously performs all operations. After completing the teaching, just give the robot a start command, and the robot will accurately complete the operation step by step according to the teaching action.
2、焊接機(jī)器人、焊接變位機(jī)及焊接夾具對(duì)焊接生產(chǎn)的影響
2. Influence of welding robot, welding positioner and welding fixture on welding production
①焊接機(jī)器人對(duì)零部件的定位精度要求較高,同時(shí)焊縫相對(duì)位置精度更高。
① Welding robot requires higher positioning accuracy of parts and higher relative position accuracy of weld.
②焊接機(jī)器人對(duì)焊接夾具前后工序的定位須一致。
② The positioning of the welding robot before and after the welding fixture must be consistent.
③由于工件都由多個(gè)簡(jiǎn)單零件組焊而成,而這些零件的裝配和定位焊,在焊接夾具上是按順序進(jìn)行的,因此它們的定位和夾緊是一個(gè)個(gè)單獨(dú)進(jìn)行的。
③ Since the workpieces are assembled and welded by multiple simple parts, and the assembly and positioning welding of these parts are carried out in sequence on the welding fixture, their positioning and clamping are carried out separately.
④由于焊接變位機(jī)翻轉(zhuǎn)的變位角度較大,焊接夾具應(yīng)盡量避免使用活動(dòng)手動(dòng)插銷。
④ Due to the large deflection angle of the welding positioner, the movable manual bolt shall be avoided in the welding fixture as far as possible.
⑤焊接夾具應(yīng)盡量采用快速壓緊件,且需配置帶孔平臺(tái)。
⑤ The welding fixture shall adopt fast compression parts as far as possible, and shall be equipped with a perforated platform.
3、焊絲對(duì)焊接機(jī)器人焊接過(guò)程的影響
3. Influence of welding wire on welding process of welding robot
開始焊接前,焊接機(jī)器人根據(jù)需求選用桶裝或盤裝焊絲。為了降低更換焊絲的頻率,建議直接選用桶裝焊絲。但由于桶裝焊絲所需的送絲軟管很長(zhǎng),且阻力大,所以對(duì)焊絲的挺度等質(zhì)量要求較高。同時(shí)盡量避免選擇鍍銅質(zhì)量稍差的焊絲,不然會(huì)使焊絲表面的鍍銅因摩擦脫落,從而造成導(dǎo)管內(nèi)容積減小,高速送絲時(shí)阻力加大,焊絲不能平滑送出,產(chǎn)生抖動(dòng),使電弧不穩(wěn),影響焊縫質(zhì)量。
Before welding, the welding robot selects barreled or coiled welding wires according to needs. In order to reduce the frequency of welding wire replacement, it is recommended to directly select barreled welding wire. However, because the wire feeding hose required for barreled welding wire is very long and has large resistance, the requirements for the stiffness and other quality of welding wire are high. At the same time, try to avoid selecting the welding wire with slightly poor copper plating quality, otherwise the copper plating on the surface of the welding wire will fall off due to friction, resulting in the reduction of the volume in the conduit, the increase of resistance during high-speed wire feeding, the welding wire can not be sent out smoothly, resulting in jitter, making the arc unstable and affecting the weld quality.
上一篇:焊接線材在焊接機(jī)器人中的作用
下一篇:自動(dòng)點(diǎn)焊機(jī)工位自動(dòng)轉(zhuǎn)換裝置介紹